The pipe market is very competitive. Pipe manufacturers are continually looking for ways to reduce cost while delivering products that meet performance expectations set by customers, codes and standards (ASTM, NSF, NEMA, etc.). Chroma Color® Corporation develops pigments/colors through internal and industry partners related to research, education, technical expertise and trade associations like the Plastic Pipe Institute (PPI) https://plasticpipe.org/index.html allows Chroma Color® to deliver superior and environmental (SUSTAINABILITY HMF) product to the pipe industry.
There are five major markets for a plastic pipe; each has its own unique needs and regulations. These five markets include:
-Building & Construction
-Drainage Pipe
-Energy Piping Systems
-Municipal & Industrial
-Power & Communications
Plastic pipe and conduit color-coded by their end-use application, such as:
-Blue = Potable Water
-White = Irrigation and Water
-Green = Sewer
-Purple (Lavender) = Reclaimed Water
-Gray = Electrical Conduit
-Orange = Telecommunication, conduit
-Yellow = Natural Gas (methane or propane) oil
-Red = Electric Power Lines, Lighting Cable
Plastic Pipe Resins:
One of the biggest challenges related to coloring a plastic pipe product is accurately matching the desired color in the specific resin. It is critical to establish a partnership with your color & additives supplier early in the development process to meet specific color and the performance attributes.
The colorant supplier must consider the unique resin, color, and performance requirements as they formulate for the application. Each resin is unique (viscosity, melt processing temperatures, natural resin color, and more). Your color supplier can assist with critical application decisions from the onset regarding the carrier resin, pigment systems, stabilizers, and other additives.
The resins primarily used for pipe include:
HDPE: High-Density Polyethylene
MDPE: Medium Density Polyethylene
PEX: Crosslinked Polyethylene
PE-RT: Polyethylene of Raised Temperature
PP-R and PP-RCT: Random Copolymerized Polypropylene
PEX-AL-PEX: Multilayer or Composite PEX Tubing
In general, the features and benefits of the high-performance high-temperature plastic-piping systems include:
- Ease of installation (Coil Pipe)
- Corrosion resistance
- Safety of potable Water
- Reliable fitting and joining options
- Lightweight, ease of transportation and handling
- Proof of long-term reliability with over decades of use around the world (100 year life expectation) with proper manufacturing and installation.
Types of Pipe and Resins
Municipal and Industrial Water Applications
For municipal and industrial applications, high-density polyethylene (HDPE) pipe is recommended. HDPE’s heat-fused joints create a leak-free pipe structure. HDPE pipe is chemical, abrasion, fatigue, seismic, and corrosion-resistant.
Conduit
High-density polyethylene (HDPE) resin is also used for the conduit to protect electrical power and telecommunications cables. It is available in long coil lengths to reduce joints and installation time. HDPE conduit is also available in a variety of sizes, colors, dimensions, and lengths. Typical applications include:
–Telecommunications
-CATV
-Highway lighting
-Underground utilities.
–Premise (Riser and Plenum) conduit has specific characteristics and flame retardant ratings for use as nonmetallic raceways in buildings.
Color Selection:
After establishing the resin, your conversation moves to color selection. Typically, your supplier has color sample chips or Pantone color charts to pinpoint the desired color for each plastic product or part.
During this selection process, colors may differ depending on gloss, grain, filler, resin type, light sources, and other factors. Knowing this in advance allows the color supplier to choose high-performance pigments that are more light stable than typical workhorse pigments.
There is also much pressure to eliminate the use of heavy metals (HM) pigments in favor of more environmentally friendly options. You need to ask your color concentrate supplier if the pellets include Heavy Metal Free (HMF)* or Heavy Metal (HM) pigments.
*Chroma Color® Corporation meets ASTM F2160 − 22 requirements that requires the use of HMF pigments and eliminates the selection of HM.
In addition, heavy metal-based heat stabilizers have traditionally been used with HDPE and/or polyethylene pipe. These include Lead and Cadmium Salts. Such environmentally unfriendly chemicals are rapidly being replaced with non-heavy metal stabilizers, such as calcium stearate.
A pipe that uses HMF (Heavy-Metal Free) stabilizers provides the end-user with the confidence of zero toxicity from heavy metals.. These include Lead and Cadmium Salts. Such environmentally unfriendly chemicals are rapidly being replaced with non-heavy metal stabilizers, such as calcium stearate. A pipe that uses HMF (Heavy-Metal Free) stabilizers provides the end-user with the confidence of zero toxicity from heavy metals.
Pipe exposed to Ultra Violet Light needs protection from the damage caused over time. Chroma Color®’s patented G series can have a stabilizer with UV resistant material to provide some protection from UV damage.
Chroma Color®’s patent G2 and G3 also provides a cost-effective solution for solid wall pipe and vibrant co-extrusion skin colors.
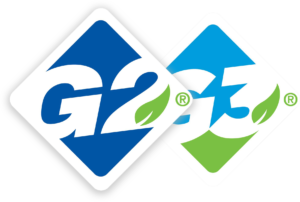
BASICS of PATENTED G2, G3 COLOR TECHNOLOGY
Highly loaded concentrates have become a cost-effective alternative to standard color products because they require less concentrate to achieve the same results and blend with resin more efficiently.
The patented G2 formulation ingredients enable Chroma Color® to boost loadings of pigments and additives up to twice what was considered feasible in traditional color and additive concentrates.
– Typically, a G2 formulation contains up to about 80% active ingredients, some as high as 85%. For some pipe applications, we can load up to 60% additives.
– A high concentration of color and additives is just one aspect of G2 technology. The technology also allows us to dial in melt flow to enable the processor to produce uniformly colored parts with color use rates as low as half a percent.
Patented G3 reduces cost and eliminates processing headaches. It achieves even more significant improvements through a total system approach. Key attributes and advantages include:
– Used with any resin system except PVC
– It delivers 20% or more increased pigment loading than G2 in Polyethylene & Polypropylene without compromising pigment dispersion and distribution
– G3 offers formulations with 40% of dyes in HIPS, PET, Nylon, Crystal Styrene, and Acrylic.
– It offers formulations with 50% or more pearlescent pigment, nearly doubling the former industry standard of 30%
-Heavy Metal Free
CHROMARK® is Chroma Color®’s laser marking additives to help control marking behavior over a broad class of resins and pigment chemistries. The Chroma Color® team can help you select the right colorant and additive package to ensure you obtain the ideal laser mark for your product at an economical cost-to-color.
With our in-house NIR Laser, we help you optimize the marking behavior and laser settings for various resins, including ABS, PE, PP, LDPE, HDPE, Co-Polyester, PBT, Polysulfone, GPPS, HDPE, Nylon, Acrylic, PVC, Polyacetal, and Polycarbonate. Besides, Chroma’s patented G3 technology can also provide highly loaded concentrates with a laser-marking additive.
Chroma Color® Plastic Pipe Case Studies
Wire and Cable Application:
A manufacturer of electrical wire was looking for a better color concentrate option for their product line. Our wire and cable research team developed a highly loaded PVC concentrate that is producing the following results:
1- Reduction in Let Down Ratio (LDR) with an LDR of 0.5% reduced inventories and upfront cost
- The low LDR reduces the number of spark outs (if any) that reduces machine downtime and increases utilization
- Black 508/2006 PVC unique formula reduced shear heat to allow increased line speeds on thin gauge products
- The unique formula enhances the black appearance on a retail shelf by giving your coiled wire a shine instead of a typical stock black dull appearance.
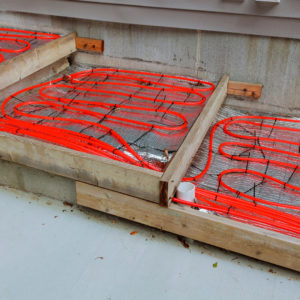
Radiant Pipe Application:
– G2 used for a high-temperature pipe used for a radiant application.
– Co-Extruded outside skin polyethylene raised temperature PERT-PE skin colors to reduce the overall cost of pipe. 3,000-4,000 of an inch thick skin
– Lower Letdown Ratios of .75% Achieved
– Red, Blue and White Colors Available
– UV additives used to prevent fading
– Other applications for this technology include high-temperature for building construction, hot and cold water pipes, and business.
Click Here To Download The Full Article As A PDF